Entre los años 2005 y 2021, siendo empleado de SIF América, trabajé en el desarrollo de diversos dispositivos de seguimiento electrónico de cargas, realizando el diseño de la electrónica, la programación de firmware, el desarrollo de back end, el diseño de la mecánica y la dirección general de los proyectos.
Este tipo de productos se utiliza para evitar el fraude fiscal, lo cual realizan trabando el acceso a la carga (generalmente trabando la apertura de la puerta, por ejemplo de un contenedor) y transmitiendo continuamente su estado general y posición geográfica a los servidores de aduanas, donde las autoridades pueden intervenir rápidamente en caso de situaciones anómalas. En la región, los países que los implementan incluyen Argentina, Uruguay, Paraguay y Costa Rica.
Además de diseñar y gestionar la fabricación de varios dispositivos, produje software de back-end utilizado en el centro de operaciones para la administración de los mismos, implementando varios protocolos de comunicación, como ser SMPP, USSD y algunos protocolos propietarios tanto bajo TCP como UDP.
A continuación resumo los puntos destacados de algunos de los dispositivos fabricados.
Dispositivo H02
En septiembre de 2005 -dando un paso al frente ante una crisis ocurrida en la empresa- tomé la responsabilidad de diseñar y producir la electrónica y el firmware para el dispositivo de seguimiento de contenedores H02, el cual había sido ya comprometido a nuestros clientes en Costa Rica. El producto tenía una fecha máxima de entrega que había que cumplir a rajatabla para evitar incurrir en fuertes penalidades contractuales.
La aduana de Costa Rica fue la segunda en Latinoamérica en implementar el sistema de seguimiento de contenedores entre puertos o diferentes zonas aduaneras. Nuestros clientes utilizaban provisoriamente un producto previo (el H01) en la espera del desarrollo específico que cumpliera con todas las regulaciones del gobierno costarricense.
En el corto período de siete meses se debía pasar del concepto al producto terminado, embalado y listo para su exportación. Se trataba de un fuerte desafío para mí, ya que no contaba con planos previos o software utilizable y no había trabajado en electrónica en muchos años.
Sin embargo, en tres meses se realizó el diseño de la electrónica y se encargaron los circuitos impresos definitivos, así como sus componentes. El firmware fue desarrollado en paralelo con el ensamblado de las placas y el montaje mecánico. Todo el ciclo se cumplió en siete meses.
El producto debía tener las siguientes características:
- Sistema completamente autónomo de control de cargas.
- Seguimiento continuo del trayecto utilizando sistema GPS.
- Reporte continuo de la posición y estado utilizando radiomódem GSM cuatribanda (SMS).
- Traba eléctrica del sello de las puertas del contenedor.
- Control electrónico de violación del sello (apertura de puerta) con aviso inmediato al servidor central.
- Resistencia a la humedad condensante de Costa Rica.
- Duración de la batería en operación continua de 14 días más 7 días de estacionamiento.
- Almacenamiento de la información durante los períodos de falta de señal, y su retransmisión automática a su recuperación.
- Capacidad de upgrade del firmware en taller.
Al evaluar las posibilidades, siendo la prioridad tener el producto en el menor tiempo posible, el diseño fue realizado con:
- Microcontrolador ARM7 LPC2138.
- Módulo de GPS ET-301.
- Módulo radiomódem para GSM Enfora GSM0108.
- Sistema electrónico de control de motores.
- Fuente de alimentación switching con protección de batería y de sobrevoltaje.
- Interface serial para la consola de comandos en taller.
- Interfaces de E/S para luces indicadoras y sensores.
- Protección ESD en todas las entradas y salidas.
- Diseño de PCBs con Protel (luego Altium).
- Fabricación de PCBs de cuatro capas.
- Componentes de montaje superficial.
- Gabinete de aluminio extruido (previamente disponible).
- Sellado con junta de goma anti-estática.
El firmware, a su vez:
- Realizado casi completamente en lenguaje C (glue code en assembler).
- Entorno multitarea utilizando FreeRTOS.
- Drivers para puertos UART, SPI, timers, E/S, librerías de file system, radiomódem, GPS, log y debug, realizados desde cero específicamente para el producto.
- Consola partida (emulación VT100) para mayor simplicidad de diagnóstico y configuración.
- Implementación explícita de los requisitos técnicos delineados por la Aduana de Costa Rica.
- Con posterioridad al lanzamiento, el firmware incorporó la capacidad de comunicación por GPRS (protocolos PPP, LCP y UDP) como alternativa al SMS en lugares donde la cobertura lo permitiera.
Mis responsabilidades en el proyecto H02 fueron:
- Definir y diseñar todos los aspectos electrónicos del producto: fuente de alimentación, módulos de GSM y GPS, microcontrolador, entradas y salidas, etc., así como el trazado del circuito impreso para su manufactura off-shore.
- Diseñar el sellado anti-humedad, conseguir proveedor y dirigir su producción.
- Encargar la provisión del circuito impreso y los componentes en los distintos proveedores.
- Supervisar el armado de las electrónicas.
- Diseñar y programar el firmware.
- Diseñar y realizar las pruebas de conformidad del producto.
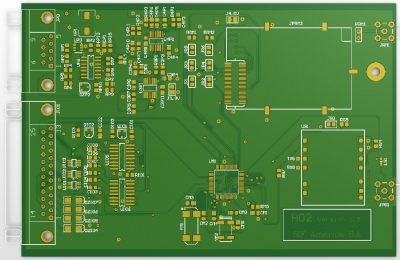
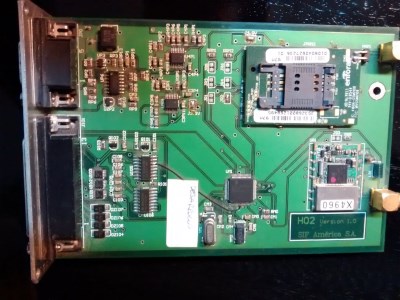
Algunas de las cosas sobre las que aprendí o expandí mis conocimientos gracias a este proyecto:
- Un montón sobre microcontroladores modernos (lo último que yo había utilizado era el venerable Z-80).
- Diseño de fuentes switching.
- Diseño de circuitos impresos.
- Protección ESD.
- Tratamiento de señales de alta frecuencia (para GPS y GSM).
- Utilización de módulos externos para GPS y GSM por medio de comandos AT y protocolo NMEA.
- Protección de transitorios.
- Diseño para bajo consumo.
- Sistema operativo FreeRTOS.
- Arquitectura de procesadores ARMv7 (registros, modos de operación, etc.).
- Búsqueda y adquisición de componentes.
- Outsourcing del ensamblado de PCBs.
Dispositivo DES3
En el año 2009 SIF América S.A. necesitaba un nuevo equipo para seguimiento de carga, el cual esta vez debía ser de corte económico, más liviano, y adaptarse a más tipos de vehículo. En esta ocasión yo quedé a cargo del proyecto, en el que no sólo diseñé la electrónica sino que también desarrollé el aparato en sí, con sus sistema de agarre, traba electrónica, etc. y dirigí todo el proceso de desarrollo y producción.
Para el control de la carga se decidió utilizar un sistema de lazo de fibra óptica, el cual -mediante ciclos alternativos de luz y oscuridad- hace imposible la creación de un “puente” que engañe al control. Asimismo, este sistema permitió una mayor flexibilidad de colocación, admitiendo incluso camiones del tipo furgón u otros que tuvieran un único barral de cierre.
El mecanismo, diseñado utilizando el software Autodesk Inventor, utilizaba un servomecanismo para trabar los punteros de la fibra óptica haciendo imposible su remoción fuera del control del software. Excepto el gabinete plástico (procurado en China), todas las piezas de la mecánica fueron fabricadas en Argentina.
Mis responsabilidades en el proyecto DES3 fueron:
- Gestionar el proyecto desde su concepción hasta su puesta en producción.
- Concebir, definir y diseñar todos los aspectos mecánicos del dispositivo, incluyendo la confección de planos.
- Definir y diseñar todos los aspectos electrónicos del producto: fuente de alimentación, módulos de GSM y GPS, microcontrolador, entradas y salidas, etc., así como el trazado del circuito impreso para su manufactura y ensamblado off-shore.
- Conseguir y coordinar proveedores, tanto de materiales como de servicios, incluyendo maquinados, corte y doblado de chapas, confección de resortes, realización de piezas de tornería, manufactura y ensamblado del circuito impreso, mazos de cables y conectores, etc.
- Supervisar el armado de la mecánica.
- Diseñar y programar el firmware, ampliando el preexistente (H02).
- Diseñar y realizar las pruebas de conformidad del producto.
- Dirigir al pequeño equipo de personas que formó parte de la producción.
Algunas de las tecnologías utilizadas para el producto fueron:
- Electrónica de diseño específico para el producto.
- Microcontrolador ARM7 LPC2387, módulo Enfora GSM0308, módulo GPS Fastrax IT520.
- Piezas estructurales de chapa de acero, cortada, plegada y punzonada.
- Pintura epoxi electroestática para las piezas externas.
- Piezas de mecanismo en resina acetal torneadas con control numérico.
- Resortes de fabricación a medida.
- Fibra óptica de 1000µm con punteros de latón.
- Gabinete estándar con sellado IP67, con maquinados de precisión para el montaje.
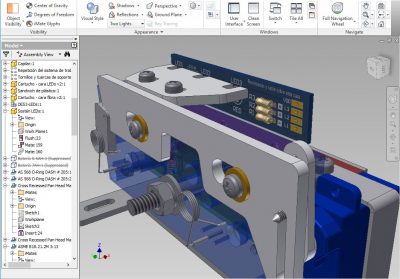
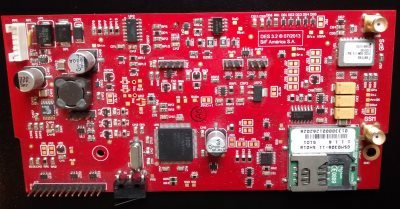
Algunas de las cosas sobre las que aprendí o expandí mis conocimientos gracias a este proyecto:
- Nuevos periféricos de los microcontroladores de la línea LPC2xxx.
- Nuevos módulos de GSM y GPS.
- Utilización de Autodesk Inventor.
- Diseño de mecanismos utilizando técnicas varias, creación de planos.
- Control de servomecanismos por PWM.
- Outsourcing de corte láser.
- Outsourcing de resortes a medida.
- Outsourcing de maquinado de partes con control numérico.
- Outsourcing de herrería (corte, plegado y soldado de chapa de acero).
- Outsourcing de serigrafía de etiquetas.
Proyecto DES4E
En el año 2013 la aduana de Uruguay inauguró el control de cargas sueltas y camiones enlonados. Para estos últimos se creó el dispositivo DES4E, el cual debía asegurarse a la parte posterior del camión y realizar el control de la carga mediante un cordón aduanero que consiste en un cable especial que recorre todo el perímetro del acoplado.
Para el diseño mecánico de este dispositivo se decidió utilizar una base en fundición de aluminio con cobertores de plástico termoformado, adquiriendo un formato estilizado y funcional.
Mis responsabilidades en el proyecto DES4E fueron:
- Gestionar el proyecto desde su concepción hasta su puesta en producción.
- Definir y diseñar todos los aspectos electrónicos del producto: fuente de alimentación, módulos de GSM y GPS, microcontrolador, entradas y salidas, etc., así como el trazado de los circuito impresos para su manufactura y ensamblado off-shore.
- Seleccionar, capacitar y supervisar al diseñador industrial encargado del diseño mecánico del producto.
- Supervisar el armado de la mecánica.
- Diseñar el cordón aduanero electrónico, seleccionar proveedor y supervisar su fabricación.
- Diseñar y programar el firmware, ampliando el preexistente (DES3).
- Diseñar y realizar las pruebas de conformidad del producto.
- Dirigir al pequeño equipo de personas que formó parte de la producción.
Algunas de las tecnologías utilizadas para el producto fueron:
- Electrónica de diseño específico para el producto.
- Microcontrolador ARM7 LPC2387, módulo Enfora GSM0308, módulo GPS Fastrax IT520.
- Base de fundición de aluminio.
- Cobertores de plástico termoformado.
- Piezas auxiliares de chapa de acero, cortada y plegada.
- Resortes de fabricación a medida.
- Cable de control aduanero con refuerzo de fibra aramida (Kevlar).
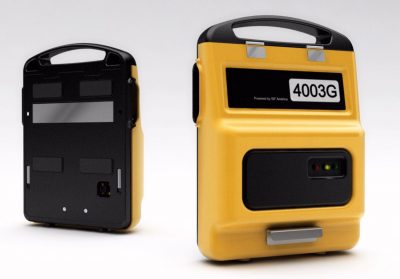
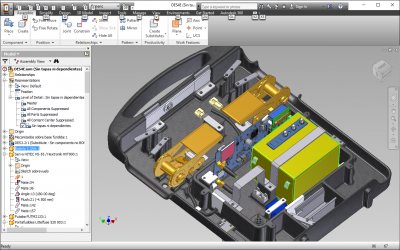
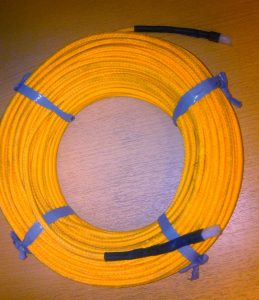
Algunas de las cosas sobre las que aprendí o expandí mis conocimientos gracias a este proyecto:
- Diseño de chasis de aluminio por colada en tierra.
- Diseño de termoformados.
- Outsourcing de termoformados.
- Outsourcing de fabricación de chasis de aluminio.
- Outsourcing de fabricación de cables especiales (fibra óptica plástica, acero).
Proyecto PEMA5
En el año 2014, con el objetivo de relanzar la operatoria de seguimiento aduanero en Argentina, se decidió producir un nuevo equipo para control de contenedores con parámetros de diseño diferentes a los utilizados para el equipo DES3.
Se trabajó esta vez con un chasis de acero inoxidable y cobertores de plástico termoformado. El mecanismo de traba y liberación contiene engranajes y otros elementos fabricados especialmente para el dispositivo.
Mis responsabilidades en el proyecto PEMA5 fueron:
- Gestionar el proyecto desde su concepción hasta su puesta en producción.
- Definir y diseñar todos los aspectos electrónicos del producto: fuente de alimentación, módulos de GSM y GPS, microcontrolador, entradas y salidas, etc., así como el trazado de los circuito impresos para su manufactura y ensamblado off-shore.
- Seleccionar, capacitar y supervisar al diseñador industrial encargado del diseño mecánico del producto.
- Diseñar el sistema de traba y liberación.
- Conseguir y coordinar proveedores, tanto de materiales como de servicios, incluyendo maquinados, corte y doblado de chapas, confección de resortes, realización de piezas de tornería, manufactura y ensamblado de los circuitos impresos, mazos de cables y conectores, etc.
- Supervisar el armado de la mecánica.
- Diseñar y programar el firmware, ampliando el preexistente (DES4E).
- Diseñar y realizar las pruebas de conformidad del producto.
- Dirigir al pequeño equipo de personas que formó parte de la producción.
Algunas de las tecnologías utilizadas para el producto fueron:
- Electrónica de diseño específico para el producto.
- Microcontrolador ARM7 LPC2387, módulo GSM SIM900, módulo GPS Maestro A2235-H.
- Base y mecanismos de acero inoxidable.
- Piezas torneadas de acero y resina acetal.
- Cobertores de plástico termoformado.
- Resortes de fabricación a medida.
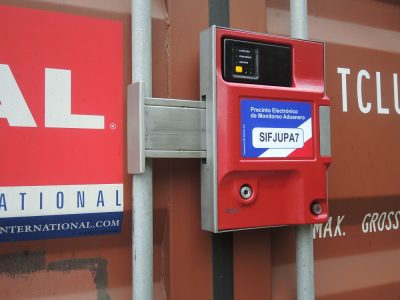
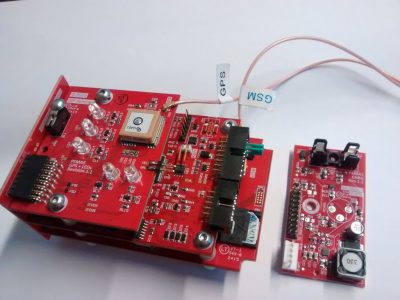
Algunas de las cosas sobre las que aprendí o expandí mis conocimientos gracias a este proyecto:
- Mejores diseños de fuentes switching.
- Carga de baterías de litio.
- Protección de baterías de litio.
- Tratamiento de metales para su endurecimiento (cementado, etc.).
- Integración de radiomódems para la utilización de la red satelital Iridium.
- Utilización de módulos 4G.
- Refinamiento en el diseño de PCBs.
- Distribución de energía.
- Diseño para la producción.